Predictive Maintenance in Mumbai: Saving Costs and Uptime with Data Analytics
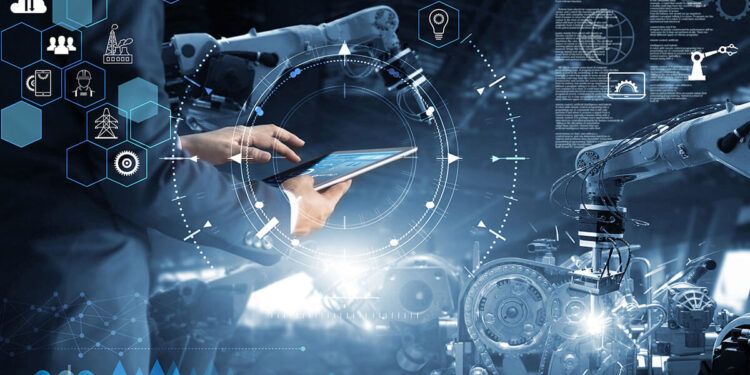
Mumbai is the beating heart of Indian manufacturing. From textiles to pharmaceuticals, automotive to consumer goods, Mumbai powers some of India’s most vital industries. But with great manufacturing prowess comes great maintenance responsibility. Unexpected equipment failures lead to costly downtime, delayed production, and safety hazards.
What if Mumbai manufacturers could look into the future and prevent these issues before they occur? With predictive maintenance (PdM), the future is now.
Moving from Reaction to Prediction
Traditionally, maintenance crews sprang into action only when an asset broke down. However, this reactive approach proved inefficient. There was no way to avoid the resulting expenses, delays, and risks by only fixing failures after the fact.
Predictive maintenance flips the script with a proactive strategy powered by data. By constantly monitoring equipment health, PdM solutions predict potential failures so manufacturers can address problems early. Instead of reacting to breakdowns, technicians stay ahead of the curve.
The results? Maximized uptime, lower costs, safer working conditions, and assets running like new for longer. Now those are manufacturing marvels Mumbai can get behind!
The PdM Advantage: Saving Time, Money, and Headaches
A critical production line goes down out of nowhere. The maintenance lead pulls her hair out, trying to track down replacement parts. Operators stand idle as output screeches to a halt. Managers scramble to reassure customers and reschedule orders.
But what if they saw this coming?
- With a predictive BA analyst course, they could’ve spotted the abnormal vibration patterns indicating imminent bearing wear.
- Instead of an unpredictable crisis, they schedule service during planned Downtime.
- No unexpected costs. No frustrated customers. No chaos.
This ability to peek into the future and turn surprises into scheduled maintenance is why PdM delivers such game-changing value:
Less Downtime = More Output
Unplanned Downtime disrupts output and delays production. With early failure detection, technicians can address issues quickly during planned maintenance periods. The result? More uptime and higher production numbers.
Fewer Surprises = Lower Costs
Equipment failures trigger emergency repairs with expensive replacement parts. PdM allows managers to control costs and optimize budgets by keeping assets in top shape.
Increased Safety
When assets operate suboptimally for too long, the results can be dangerous. Failures like ruptured valves or ruptured tanks put workers at risk. With PdM, facilities can fix minor problems before they escalate into health hazards.
Extended Equipment Life
By keeping equipment tuned and calibrated, PdM ensures assets run within safe operating parameters for as long as possible. Plants can delay end-of-life retirements and replacement costs.
Data: The Driving Force Behind PdM
Predictive maintenance runs on data. Sensors embedded throughout facilities keep a constant pulse on equipment health. Critical metrics like vibration, temperature, pressure, flow rate, and power consumption provide insight into developing issues.
Feed this monitoring data into advanced analytics software; algorithms can translate numbers into failure risk forecasts. Data is the universal language that helps humans understand machine needs.
So for Mumbai manufacturers ready to leap, step one is building a data-driven foundation with:
- Industrial Internet of Things (IIoT) sensors
- Secure data collection infrastructure
- Centralized data lakes for storage and access
- Analytics interfaces for data modeling
With sweeping digitization initiatives like Industry 4.0, Mumbai’s industries can access helpful resources like analytics talent and affordable sensor equipment. The drive for smart factories fortifies the bedrock manufacturers’ need for scalable success with predictive maintenance programs.
Making the PdM Vision a Reality
Implementing PdM requires much more than just enabling some sensors. At its core, predictive maintenance allows teams to translate data into decisions. Several key ingredients must come together to close the loop from detection to action.
Ingredients for PdM Success
1. Cross-Functional Teams
Data scientists interpret sensor signals, engineers understand asset subtleties, and technicians keep operations humming. All roles must unite within asset performance management command centers for holistic decision-making.
2. Change Management
For many maintenance teams, PdM requires new processes and skill sets. Proper change management ensures teams have the training and leadership support needed to implement predictive insights.
3. Edge Computing Infrastructure
With distributed sensor networks and enormous data flows, edge computing allows assets to operate semi-autonomously while enabling centralized analytics. Real-time local business analysis course coupled with cloud data processing powers rapid failure forecasting.
4. Data Contextualization
Alone, sensor measurements provide limited value. By integrating signals with asset histories, runtimes, work order logs, and event data, PdM contextualizes discrepancies within a machine’s unique experience for smarter predictions.
5. Regulation-Compliant Cybersecurity
With reams of data moving across networks, security is paramount, especially for regulated industries. Encryption, access controls, and data integrity measures provide peace of mind around safety and compliance.
PdM in Action: Mumbai Manufacturing Success Stories
Global best practices provide helpful blueprints, but homegrown success stories deliver the most impactful inspiration. Across Mumbai’s key sectors, leaders have already built benchmarks with stellar results:
Textiles – Maximizing Uptime, Optimizing Maintenance
Using vibration data analytics, a fabric mill predicted bearing failures on critical weaving equipment. Instead of reacting to 15 breakdowns per month, the mill schedules predictive maintenance during planned outages to identify emerging issues early.
Results:
- 65% reduction in unplanned Downtime
- 25% increase in fabric output
- 20% lower annual maintenance costs
Automotive – Improving Quality Control
A major auto parts supplier uses temperature and vibration monitoring to detect subtle process deviations on a production line. By catching defects sooner, engineers adjust tools preemptively to improve product quality and yield.
Results:
- 32% reduction in quality rejects
- 4% increase in annual production numbers
- $120,000 saved from scrap reduction
Pharmaceuticals – Ensuring Safety and Compliance
Leveraging pressure sensors and shearing profiles, a vaccine production facility anticipated overheating issues on a critical lyophilized vial sealing unit. Instead of mid-run failures, staff could proactively calibrate thermal controls to avoid compliance violations.
Results:
- No product losses from seal defects
- No regulatory compliance observations
- 6 critical safety incidents avoided
These examples provide a glimpse into the operational excellence Mumbai manufacturers can achieve using data to predict problems, not just react to them.
PdM Brings a Bright Future for Mumbai Industry
Predictive maintenance heralds a new era for Mumbai on its journey to become a global manufacturing powerhouse. However, successful adoption at scale requires cross-industry collaboration.
Forward-thinking companies must lead the charge in showing what PdM makes possible. Government agencies can support technology pilots and skills training for assets crucial for public services. Industry associations must promote knowledge sharing on predictive best practices across sectors.
Together, Mumbai’s manufacturing community can build a thriving ecosystem where assets operate reliably for decades, technicians work confidently using machine insights, and products progress smoothly from order to output.
Instead of dreading downtime surprises, companies can feel empowered, in control, and ready for the future. That is the transformational impact predictive maintenance gives Mumbai industries the power to achieve.
Business name: ExcelR- Data Science, Data Analytics, Business Analytics Course Training Mumbai
Address: 304, 3rd Floor, Pratibha Building. Three Petrol pump, Lal Bahadur Shastri Rd,
opposite Manas Tower, Pakhdi, Thane West, Thane, Maharashtra 400602
Phone: 9108238354, Email: [email protected]